Manufacturing Process Quality Engineer
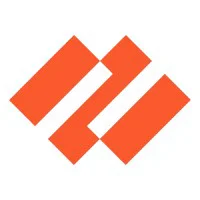
Palo Alto Networks
Summary
Join Palo Alto Networks as an Experienced Process Quality Engineer to optimize manufacturing processes, troubleshoot production bottlenecks, and drive measurable improvements. This role requires expertise in process control, continuous improvement, industrial engineering, and quality engineering. You will serve as the point of contact for factory quality and process issues, ensuring timely resolution and coordination across teams. The position demands a results-oriented professional capable of driving tasks to completion and ensuring alignment between factory teams, suppliers, and stakeholders. You will be responsible for production and process improvement, quality engineering and RCA, testing, inspection and compliance, and quality metrics and reporting. The ideal candidate will have a Bachelor's or Master's degree in a related field and 5+ years of experience in hardware manufacturing, quality engineering, or process improvement roles.
Requirements
- Bachelorโs or Masterโs degree in Mechanical Engineering, Industrial Engineering, Manufacturing Engineering, or a related field
- 5+ years of experience in hardware manufacturing, quality engineering, or process improvement roles
- Strong knowledge of PCBA manufacturing techniques, materials, and process controls
- Expertise in RCA, CAR, and quality engineering methodologies
- Hands-on experience with Lean, Six Sigma, SPC, FMEA, and 8D problem-solving tools
- Experience with test and inspection methodologies for high-quality hardware production
- Excellent analytical, problem-solving, and communication skills
- Ability to work remote and cross-functionally with engineering, production, and quality teams
Responsibilities
- Production & Process Improvement: Identify and resolve bottlenecks, optimize workflows, and maintain process control for stability
- Quality Engineering & RCA: Lead Root Cause Analysis (RCA) investigations, implement Corrective and Preventive Actions (CAPA), and use tools like FMEA, 8D, and 5-Whys for continuous improvement
- Testing, Inspection & Compliance: Standardize processes across sites, escalate quality issues, ensure proper CAPA implementation, and drive top-issue reduction
- Quality Metrics & Reporting: Monitor and improve metrics such as FPY goals, Bonepile, and CAPA effectiveness, ensuring data accuracy and integrity
- Collaboration & Escalation: Participate in weekly quality meetings, follow up on action items, and work closely with cross-functional teams to resolve design, production, and customer-related issues
Benefits
The offered compensation may also include restricted stock units and a bonus